Unlocking the Secrets of Continuous Duty Solenoids
Ever wondered about the magic behind devices that provide a constant pull or push? From industrial automation to everyday appliances, continuous duty solenoids are the unsung heroes of electromechanical systems. These compact powerhouses convert electrical energy into a constant linear force, making them essential components in a wide range of applications.
So, how does a continuous duty solenoid actually work? At its core, it's a fascinating interplay of magnetism and electricity. A continuous duty solenoid, unlike its intermittent counterpart, is designed to remain energized for extended periods. This seemingly simple functionality requires careful engineering to manage heat dissipation and ensure reliable, long-term operation.
The basic principle is similar to other solenoid types. A coil of wire surrounds a movable iron core or plunger. When an electric current passes through the coil, it generates a magnetic field. This field pulls the plunger inwards, creating the linear force. The continuous duty solenoid is engineered to hold the plunger in this position as long as the current flows, allowing for extended activation.
The history of solenoids traces back to the early 19th century with the discovery of electromagnetism. Initially used in telegraphs and other signaling devices, solenoids have evolved significantly. The development of continuous duty solenoids marked a crucial step, enabling their use in applications requiring sustained force, like industrial valves and locking mechanisms.
Understanding continuous duty solenoid operation is key to selecting the right solenoid for a specific application. Factors like required force, stroke length (the distance the plunger travels), duty cycle, and operating voltage are critical considerations. Neglecting these aspects can lead to overheating, premature failure, or simply an ineffective system.
A critical issue with continuous duty solenoids is heat management. Since they are designed for prolonged operation, they generate significant heat. Efficient heat dissipation is paramount to prevent damage and ensure longevity. This is typically achieved through design features like specialized coil materials and integrated cooling mechanisms.
One clear benefit of a continuous duty solenoid is its ability to maintain a constant force for extended durations. This is essential for applications such as holding valves open or closed in industrial processes. Another advantage is their relatively simple design and control, making them easy to integrate into various systems.
Consider the example of a hydraulic valve in a manufacturing plant. A continuous duty solenoid can precisely control the flow of hydraulic fluid, maintaining a consistent pressure for critical operations. Similarly, in medical equipment, these solenoids can regulate fluid flow in pumps or control the position of surgical instruments.
Effective implementation of continuous duty solenoids often involves careful selection based on load requirements, power source considerations, and environmental factors. Regular maintenance, including cleaning and inspection, is essential for optimal performance.
Advantages and Disadvantages of Continuous Duty Solenoids
Advantages | Disadvantages |
---|---|
Constant force for extended periods | Heat generation requiring management |
Relatively simple design and control | Can be less energy-efficient than intermittent solenoids |
Versatile application in various industries | Susceptible to damage from overheating if not properly cooled |
A real-world example is the use of continuous duty solenoids in industrial printers. They control the precise movement of print heads, ensuring accurate ink deposition for high-quality output.
Another example is in automotive applications, where these solenoids are used in locking mechanisms for doors, trunks, and fuel caps, providing reliable and secure operation.
Overheating is a common challenge with continuous duty solenoids. Ensuring adequate heat dissipation through proper cooling mechanisms is crucial.
Frequently Asked Questions:
1. What's the difference between a continuous duty and an intermittent duty solenoid? Continuous duty solenoids can stay energized indefinitely, while intermittent ones are designed for short bursts of activation.
2. How do I choose the right solenoid for my application? Consider force, stroke length, duty cycle, and voltage requirements.
In conclusion, the continuous duty solenoid stands as a testament to the power of electromagnetism. Its ability to provide a constant, controlled force makes it indispensable across a wide range of industries. From manufacturing and automation to medical devices and consumer electronics, the continuous duty solenoid is silently empowering our modern world. By understanding the principles of its operation, its benefits, and the key considerations for successful implementation, we can harness the full potential of this remarkable technology.
Ignite your spirit exploring phoenix tattoo designs
Unlocking design harmony with briarwood benjamin moore color pairings
Unraveling the mystery of aftermarket car stereo wire colors

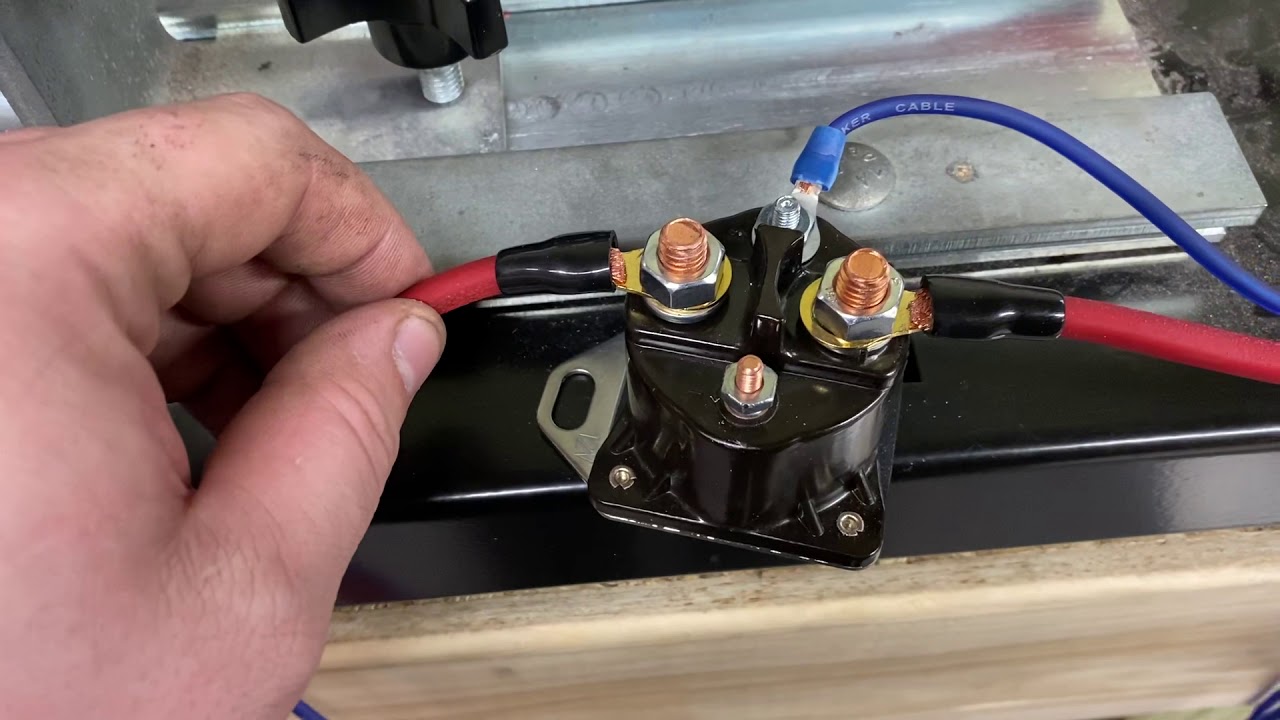





